March 24, 2011
featured blogs
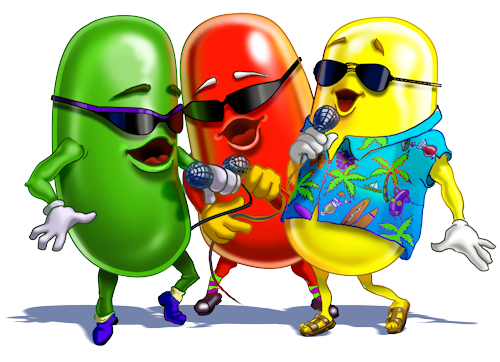
May 2, 2024
I'm envisioning what one of these pieces would look like on the wall of my office. It would look awesome!...
Apr 30, 2024
Analog IC design engineers need breakthrough technologies & chip design tools to solve modern challenges; learn more from our analog design panel at SNUG 2024.The post Why Analog Design Challenges Need Breakthrough Technologies appeared first on Chip Design....